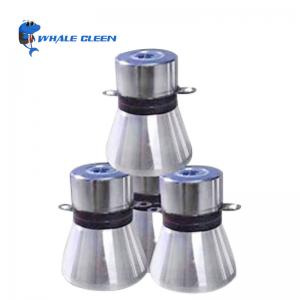
Add to Cart
Ultrasonic Vibrator For Ultrasonic Cleaning Machine With 50W~100W Ultrasonic Power
THE ULTRASONIC TRANSDUCER
Sound that is generated above the level of human hearing range is called ultrasound. Although ultrasound typically starts at 20 KHz, most ultrasonic transducers start at 200 KHz. Ultrasound, which is similar in nature to audible sound, has far shorter wavelengths and is far more suitable to detect small flaws. These shorter wavelengths are what make ultrasound and ultrasonic transducers extremely useful for nondestructive testing and measurement of materials.
An ultrasonic transducer itself is a device that is capable of generating and receiving ultrasonic vibrations. An ultrasonic transducer is made up of an active element, a backing, and wearplate. The active element is a piezoelectric or single crystal material which converts electrical energy to ultrasonic energy. It will also then receives back ultrasonic energy and converts it to electrical energy. The electrical energy pulse is generated from an instrument such as a flaw detector.
The backing is most commonly a highly attenuative and very dense material and is used to control the vibration of the transducer crystal by absorbing the energy that radiates from the back face of the piezoelectric element. When the acoustic impedance of the backing material matches that of the piezoelectric crystal, the result is a highly damped transducer with excellent resolution. By varying the backing material in order to vary the difference in impedance between the backing and the piezoelectric crystal, a transducer will suffer somewhat and resolution may be much higher in signal amplitude or sensitivity.
The main purpose of the wearplate is simply to protect the piezoelectric transducer element from the environment. Wearplates are selected to generally protect against wear and corrosion. In an immersion-type transducer, the wearplate also serves as an acoustic transformer between the piezoelectric transducer element and water, wedge or delay line.
For the conditions under which ultrasonic cleaning devices are operated, pre-stress of less than approximately 30 MPa usually is sufficient to protect the ceramic components of the transducer. On the other hand, if the prestress is too low, excessive mechanical losses at the ceramic / metallic interfaces can reduce efficiency. Pre-stress can be estimated by using a torque wrench, calibrated against charge, to tighten the bolts. This measuring method is simple, but it is not the most accurate, and consequently it is recommended primarily for production-run transducers for which the variations among corresponding components are, hopefully, minimal. The more accurate way of measuring pre-stress is to measure the charge generated in the ceramic elements under short circuit conditions. A capacitor connected to the transducer’s electrical terminals and to a direct current voltmeter facilitates measurement of the charge as each bolt is tightened.
In ultrasonic cleaning applications, effects of the dimensions and configuration of the water tank, the water load, and the thickness of the bonding layer affixing the transducer to the water tank combine to slightly reduce the frequency of the transducer, and give rise to several additional resonances. Despite these negative factors, however, a well-designed transducer, incorporated in a well-designed circuit, will operate near its resonance frequency.
Cavitation occurs when the vibration of a transducer surface interfacing with a liquid (usually water, but possibly a water / organic solvent mixture in an ultrasonic cleaning application) is sufficient to create a partial vacuum that exceeds the vapor pressure of the liquid, and bubbles form at the vibrating surface. Cavitation is a desirable feature in ultrasonic cleaning or liquid vaporizing applications, but obviously must be avoided in signal transmission applications. At atmospheric pressure, and with water alone as the interfacing liquid, the threshold forcavitation, pC0 (bar), is:
Equation 5.9
pC0=(0.00025ƒ)2 + (0.045ƒ-1)
For frequencies from kilohertz to several hundred kilohertz (2). If the transducer is submerged, and the vibrating surface is several meters or more below the atmosphere / liquid interface, the threshold for cavitation increases to:
Equation 5.10
pCh=pC0 + 0.10h
where
pCh= threshold for cavitation in atmospheres at depth h in meters (bar)
pC0= threshold for cavitation at zero depth (bar)
Cavitation (J) can be initiated when the acoustic intensity at the vibrating surface, in W/cm2, is:
Equation 5.11
J=0.15(pC0 + 0.10h)2
The acoustic intensity at the vibrating surface can be determined from: (acoustic output power of transducer) (surface area of transducer). In application, however, because the threshold for cavitation is affected by the characteristics of the transducer (signal frequency, acoustic pulse length, acoustic uniformity / non-uniformity of the vibrating face) and by various conditions (depth of submersion, temperature, dissolved air content of the liquid), cavitation may not be initiated until the acoustic intensity is significantly higher, e.g., between 0.3 (PC0 +0.10h)2 and 0.4 (PC0 + 0.10h)2.
Specification:
Model | Z-X18 |
Tank Capacity | 53Liter |
Tank Size | 500*350*350mm |
Unit Size | 640*490*570mm |
Packing Size | 810*620*910mm |
Frequency | 40KHz |
Ultrasonic Power | 900W |
Heating Power | 1500W |
Cleaning Time Setting | 1-99H Adjustable |
Temperature Range | 20-95C Adjustable |
FAQ:
1. What Can I Clean Using Ultrasonic Cleaners?
Metals such as gold and platinum are safe to clean with ultrasonic devices.
Hard natural gemstones can also be put into an ultrasonic cleaner provided that they have few inclusions and have not been treated with heat or chemicals.
Anyway, be sure to ask the jeweler at the time you purchase any piece of jewelry whether it can be cleaned with an ultrasonic cleaner.
There might be unsuitable alloys or gems, or some gemstones may have been treated, becoming more vulnerable in the process.
2. Can ultrasonic cleaning damage parts?
Ultrasonic cleaning is considered safe for most parts; although in some cases it is necessary to observe caution. Although the effect of thousands of implosions per second is very powerful, the cleaning process is safe.